Understanding what conveyor downtime is actually costing your company is essential to providing a long-term strategy that empowers your team to not only be more productive, but more cost-effective. On the surface, it’s easy to consider the belt cost and the labor of the installation crew, but only taking these factors into consideration can leave out a significant portion of the total cost.
By acknowledging the issues associated with conveyor belt downtime, whether that be product loss, missed deadlines, labor loss, or the need for belt repair, managers put themselves in a better position to minimize the negative impact on production flow in a proactive way. In doing so, you empower your maintenance crew with more timely and routine repairs, harbor a safer work environment that ensures your equipment and machinery will last longer, and significantly reduce downtime and overtime costs.
Invest in savings
Now, the initial investment may cause some sticker shock, and we get that. But, when you consider the extended downtime that is created with waiting for the arrival of the installation crew and all of the valuable production loss that is subsequently created, the true realization of an ROI is very short. Typical costs of downtime at food production facilities can range from $20K-$50K or more per incident. This just goes to show you that the savings of owning your own high speed belt splicing equipment can add up quickly!
How much can you save by handling in-house splicing? Here’s an example:
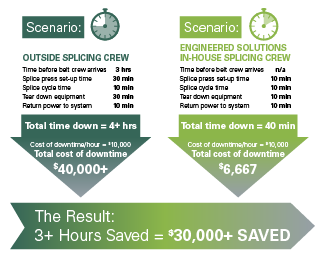
Bringing your splicing processes in-house results in massive savings compared to third-party solutions.
Imagine never having to bring an outside crew in to splice your conveyor belts again and taking charge of your own destiny. By bringing belt splicing technology in-house, you allow yourself to schedule your maintenance tasks according to your production’s needs with a quick, consistent, and quality process that fixes your conveyor belt every time.
How (and why) it works
Portable splice presses have come a long way. Through extensive research and development, splicing technology now utilizes intuitive controls to facilitate process-driven solutions that even allow beginners to produce professional-grade splices time and time again. Additionally, recipe storage in ergonomic interfaces eliminates steps like setting time, temperature, and pressure. Some equipment even provides contactless heating, which includes preheating stages that effectively eliminate moisture and potential pinholes that can weaken splices, and harbor dirt and bacteria.
Furthermore, the air-cooling technology in some of these units means that no outside tanks or water sources are needed, drastically reducing set-up and tear-down time, as well as overall splice time and incident costs. From a sanitation perspective, this helps to eliminate cross contamination concerns that may be a result of external water sources coming into contact with production equipment.
Bring it in
If you are interested in seeing how a large confectionary plant benefitted from using Flexco technology, check out our latest Food Processing Application Story. Also, if you would like more details on how you can save even more time and money, I would encourage you to download a copy of our free e-book, “In-House Belt Splicing: Limiting Downtime in your Food Processing Plant.”
Better yet, have a Flexco representative visit your site to show you just how quick and easy it is to get your operation back up and running in a fraction of the time it takes using an outside service provider. Click here to set up an onsite demo of our game changing equipment.
Request Onsite Product Demo
Authored by: Jonathan Morgan, Industry Manager – Food Processing
As an Industry Manager at Flexco, Morgan focuses on the food processing industries, including proteins, baking, and produce. Morgan has a mechanical engineering education, application knowledge, extensive industry network, and technical sales support experience.